Étude co-réalisée par CORETEC et le CETIAT : récupération & valorisation de chaleur fatale en sidérurgie
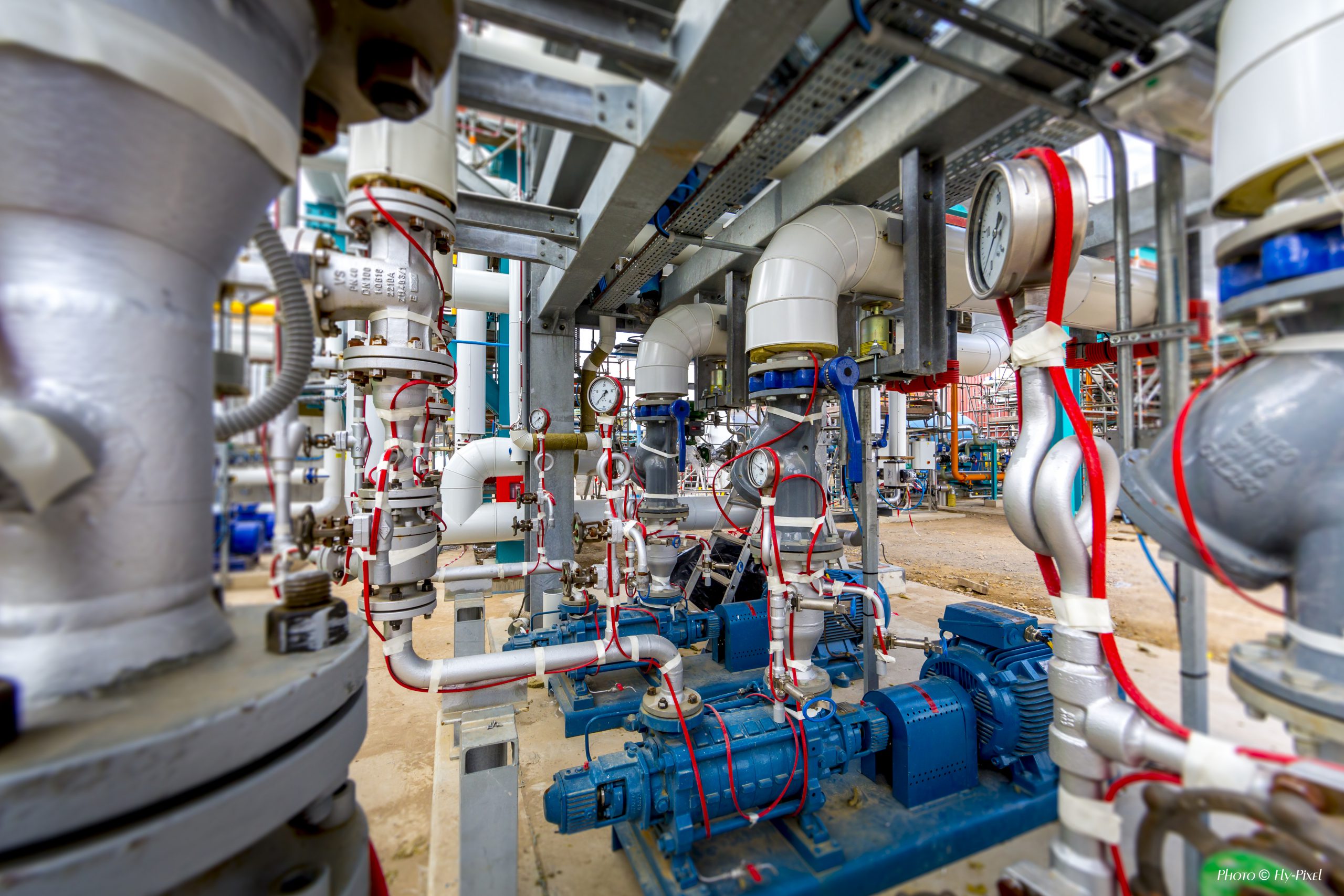
Découvrez un panel de solutions de décarbonation pour une usine sidérurgique !
CONTEXTE
Le site étudié est un site de production métallurgique important.
Son processus de fabrication nécessite une consommation énergétique annuelle conséquente, notamment au niveau des cuves d’électrolyse et des fours.
La valorisation des pertes énergétiques devient un enjeu environnemental indispensable.
Pour poursuivre leurs efforts, les responsables techniques souhaitaient étudier les opportunités de récupération et valorisation, en interne et en externe, de la chaleur fatale disponible sur les installations de l’usine. Grâce à la complémentarité de leur expertise et appuyés sur des collaborations précédentes réussies, CORETEC et le CETIAT ont donc remporté ensemble l’Appel d’Offre de l’industriel.
PARTIES PRENANTES
Le CETIAT est un centre technique indépendant, qui accompagne les industriels dans leurs projets d’innovation, de transition écologique et énergétique, de décarbonation des procédés thermiques, de qualité d’air intérieur et métrologie de l’énergie. Pour cela, ils réalisent des études, essais et formations de la conception à la mise sur le marché.
CORETEC accompagne les sites industriels, les acteurs du secteur des déchets et les infrastructures, sur les installations de production d’utilités process, l’optimisation énergétique et la décarbonation des utilités, en phase d’Expertise, d’Ingénierie d’avant-projet et de Réalisation en conception/construction.
CADRE DE L’ÉTUDE
L’objectif de la mission est de définir techniquement et économiquement les solutions les plus pertinentes pour le site industriel concerné.
PÉRIMETRE TECHNIQUE
Lors d’un audit énergétique basé sur des interventions sur le site et sur des données énergétiques issues de la certification ISO 50 001, le CETIAT a tout d’abord inventorié toutes les sources et puits de chaleur afin d’identifier les actions de valorisation énergétique les plus pertinentes et de définir les couplages sources / besoins de chaleur.
A l’issue de cette étude, 6 solutions de valorisation ont été proposées :
- Alimenter un système de production d’électricité type ORC ou turbine, c’est-à-dire mettre en place une transformation mécanique de la chaleur pour produire de l’électricité,
- Substituer le système de chauffage des locaux,
- Préchauffer de l’air comburant,
- Préchauffer des pièces avant traitement,
- Chauffer un flux chaud type boucle fluide thermique,
- Substituer une boucle de refroidissement existante.
Après cette première étape, CORETEC a étudié les solutions techniques permettant la mise en œuvre de ces couplages et a défini les solutions de récupération et valorisation de chaleur à sélectionner. Cela, en tenant compte des différentes dimensions : faisabilité technique, performance énergétique, investissement financier et perspectives de retour sur investissement.
FOCUS SUR L’ÉTUDE REALISÉE
ÉTAT DES LIEUX DU SITE
Des sources et puits de chaleur ont été identifiés par le CETIAT pour récupérer et valoriser la chaleur perdue. Cela, dans l’objectif de diminuer l’impact environnemental du site, en réduisant son empreinte carbone.
SOURCES DE CHALEUR IDENTIFIÉES
Une quantité considérable de chaleur perdue a été identifiée, représentant plus de 20% de la consommation de l’usine.
Les principales sources sont les :
- Fumées des différents types de fours,
- Fumées process,
- Rejets d’eaux chaudes.
PUITS IDENTIFIÉS
L’étude du CETIAT a permis de définir qu’environ 10% de la chaleur pouvaient être valorisés sur le site, ce qui équivaut à environ 2% de la consommation de l’usine. Les puits de chaleurs les plus qualitatifs sont les suivants :
- Chaudière fluide thermique : 4GWh
- Chauffage des locaux : 2GWh
- Préchauffage de l’air comburant de 2 fours : 5GWh
Enfin, d’autres solutions existent, comme l’installation de modules ORC qui permet de produire de l’électricité avec une source de chaleur à basse température.
Une autre solution de valorisation peut également être envisagée en externe. En effet, le site industriel pourrait injecter sa chaleur récupérée à hauteur de 14GWh/an, directement sur un réseau de chauffage urbain à créer à proximité.
SOLUTIONS PROPOSÉES
Les bilans thermiques réalisés par le CETIAT ont permis de qualifier chaque source et puit et de proposer différents couplages. Les solutions les plus pertinentes de récupération et valorisation de chaleur fatale, qui ont été retenues pour l’étude d’avant-projet, sont les suivantes :
- Fumées issue des fours de l’atelier fonderie pour substituer l’utilisation de la chaudière fluide thermique,
- Fumées process pour produire de l’électricité avec un module ORC, et/ou alimenter le RCU,
- Compresseurs d’air pour alimenter une partie de la production d’eau chaude de l’usine,
- Fumées d’un four complexe pour alimenter le chauffage interne de l’usine.
AVANT-PROJET DES SOLUTIONS
Les solutions ayant été clairement identifiées lors de la première partie de l’analyse du site, CORETEC a ensuite réalisé une étude de faisabilité technique et financière des systèmes de récupération définis précédemment.
SOLUTION – FUMÉES DES FOURS DE L’ATELIER FONDERIE
Objectif : Valorisation de l’énergie pour substituer une production de chaudière
Principe de la solution :
Mise en place d’une boucle pour alimenter la chaudière fluide thermique.
Les fumées des fours sont captées par des hottes, puis baissées en température. Elles sont ensuite collectées dans des gaines communes jusqu’à un échangeur de 700kW qui les baissera encore en température, pour les évacuer par une cheminée extérieure.
Ce passage de fumées dans l’échangeur permettra de réchauffer les retours provenant d’autres lignes de production, ce qui diminuera la consommation de la chaudière fluide thermique. La chaudière reste tout de même en support lorsque l’énergie nécessaire n’est pas suffisante avec les fumées des fours de fonderie.
Schéma de principe de la solution :
Une solution qui permet un gain énergétique d’environ 4GWh/an, soit une économie financière d’environ 290k€ par an.
Côté environnement, elle permet d’éviter l’émission de 215 tonnes de CO2 chaque année.
Au niveau du budget, elle représente un CAPEX d’environ 1 500k€, avec une aide Fonds Chaleur estimée à hauteur de 15%, soit 230k€, pour un TRI inférieur à 5 ans.
*Coût du gaz naturel estimé à 31 €/MWh et électricité à 70 €/MWh
SOLUTION – FUMÉES PROCESS
Objectif : Valorisation de l’énergie vers un module ORC et/ou un RCU
Principe de la solution :
Mise en place d’une boucle d’eau chaude pour alimenter un module ORC et/ou le RCU de la ville.
Ici, il s’agit de capter les fumées de process avant le traitement de celles-ci. Elles sont ensuite abaissées en température lors de leur passage dans un échangeur pour chauffer une boucle d’eau. Une partie de cette eau chaude sera utilisée pour la chauffe d’un futur réseau de chaleur urbain et l’autre servira à la production d’électricité via un module ORC. Il est prévu que le surplus d’énergie soit dissipé avec un aéroréfrigérant.
Deux variantes de collecte des fumées sont envisagées pour cette solution :
- Système de récupération avec un échangeur commun,
- Système de récupération unitaire avec un échangeur à chaque sortie.
Schéma de principe de la variante 1 – échangeur commun :
Cette première variante ne possède qu’un seul échangeur et nécessite de calorifuger les gaines de collecte des fumées pour éviter la dissipation thermique avant l’entrée dans l’échangeur.
Une solution qui permet un gain énergétique d’environ 18GWh/an, soit une économie financière d’environ 540k€ par an.
Côté environnement, elle permet d’éviter l’émission de 3 650 tonnes de CO2 chaque année.
Au niveau du budget, elle représente un CAPEX d’environ 5 750k€ avec une aide Fonds Chaleur estimée à hauteur de 15%, soit 860k€, pour un TRI de 9 ans.
*Prix de revente au RCU estimé à 30 €/MWh et de l’électricité green PPA à 120 €/MWh
Schéma de principe de la variante 2 – échangeurs unitaires :
La deuxième variante permet d’être au plus proche des cuves et d’éviter de calorifuger les gaines communes de captation pour éviter la dissipation thermique. Le fonctionnement reste similaire entre les deux variantes mais la deuxième permet d’avoir un système plus simple.
Cependant, l’installation de plusieurs échangeurs entraîne un coût plus élevé.
Une solution qui permet un gain énergétique (thermique et électrique) d’environ 20GWh/an, soit une économie financière d’environ 690k€ par an.
Côté environnement, elle permet d’éviter l’émission de 3 800 tonnes de CO2 chaque année.
Au niveau du budget, elle représente un CAPEX d’environ 7 800k€ avec une aide Fonds Chaleur sur le RCU estimée à hauteur de 15%, soit 860k€, pour un TRI inférieur à 9 ans.
*Prix de revente au RCU estimé à 30 €/MWh et de l’électricité green PPA à 120 €/MWh
SOLUTION – CHALEUR COMPRESSEURS D’AIR
Objectif : Substitution de la production de chauffage au fioul pour alimenter le chauffage des locaux
Principe de la solution :
Création d’une boucle d’eau chaude basse température pour alimenter le chauffage d’une partie des locaux de l’usine.
Pour chauffer cette boucle d’eau, on peut récupérer la chaleur générée par des compresseurs d’air. Actuellement, ils sont refroidis en circuit fermé avec de l’eau industrielle, mais la solution propose de modifier ce fonctionnement pour utiliser la chaleur. Ainsi, le système de refroidissement des compresseurs sera ajusté pour passer à un régime 40/65°C. Un échangeur de chaleur sera installé en sortie de la boucle de refroidissement des compresseurs, permettant de récupérer l’énergie.
Une liaison eau chaude sera ensuite créée entre les compresseurs et les réseaux existants des bâtiments pour alimenter les locaux.
Les anciens équipements de l’usine seront conservés en appoint/secours si la puissance récupérée sur les compresseurs est inférieure à la demande du réseau.
Schéma de principe de la solution :
Une solution qui permet un gain énergétique (thermique et électrique) d’environ 1GWh/an, soit une économie financière d’environ 115k€ par an.
Côté environnement, elle permet d’éviter l’émission de 400 tonnes de CO2 chaque année.
Au niveau du budget, elle représente un CAPEX d’environ 430k€, pour un TRI inférieur à 4 ans.
*Coût du gaz naturel estimé à 31 €/MWh, du fioul à 69€/MWh et de l’électricité à 42€/MWh
SOLUTION – FUMÉES D’UN FOUR COMPLEXE
Objectif : Alimenter le réseau de chauffage interne de l’usine
Principe de la solution :
Création d’une boucle de chaleur basse température pour alimenter le chauffage des bâtiments de l’usine.
Les fumées du four seront captées, avant le traitement de fumées, pour être abaissées en température. Pour cela, elles passeront par un échangeur, ce qui permettra de chauffer une boucle d’eau, tout en abaissant les températures des fumées. La chaleur, ainsi valorisée sous forme d’eau chaude, permettra d’alimenter les différents bâtiments de l’usine.
L’installation de nouveaux émetteurs pourra être prévue pour les réseaux n’étant pas adaptés à l’alimentation en eau chaude.
Schéma de principe de la solution :
Une solution qui permet un gain énergétique d’environ 2,2GWh/an, soit une économie financière d’environ 225k€ par an.
Côté environnement, elle permet d’éviter l’émission de 720 tonnes de CO2 chaque année.
Au niveau du budget, elle représente un CAPEX d’environ 1 380k€, avec une aide Fonds Chaleur estimée à hauteur de 15%, soit 200k€, pour un TRI d’environ 5 ans.
*Coût du gaz naturel estimé à 31 €/MWh, du fioul à 69€/MWh et de l’électricité à 42€/MWh
FINANCEMENT & BUDGET
SUBVENTIONS
APPEL A PROJETS FONDS CHALEUR de l’ADEME
L’AAP FONDS CHALEUR accompagne le financement des installations de production de chaleur renouvelable et de récupération de chaleur fatale, mais aussi des réseaux de chaleur/froid liées à ces installations.
Pour y être éligible, le projet doit avoir fait l’objet d’une étude énergétique récente (moins 2 ans) et valoriser une quantité d’énergie thermique supérieure à 1GWh/an.
Le FONDS CHALEUR permet d’obtenir jusqu’à 30% du montant du projet en subventions, pour les grandes entreprises. L’aide est modulée afin de respecter un temps de retour brut supérieur à 24 mois après versement des aides de l’ADEME.
L’éligibilité de ce projet à FONDS CHALEUR dépend du coût de la vapeur pris en compte et de l’économie de CO2 générée. Raisonnablement, on évalue à 15% le taux de subvention de ce genre de projet.
BILAN : tableau de synthèse chiffré
CONTINUITÉ DU PROJET
A l’issue de cette étude, menée en collaboration par le CETIAT et CORETEC, le client dispose d’un bilan complet chiffré de son site industriel en termes de récupération de chaleur. Il bénéficie également d’une connaissance précise des sources et puits de chaleur depuis l’analyse fine des données d’entrée, jusqu’à la proposition pragmatique des solutions possibles et des potentiels de gain.
Véritable outil de prise de décision, l’étude lui permet de choisir les projets qu’il va mettre en œuvre, en fonction de ses enjeux énergétiques, de sa feuille de route décarbonation, du potentiel estimé de chaque projet, mais aussi de leur complexité technique et de leur impact financier et environnemental.
Dans un 2ème temps, une fois les décisions et les budgets associés actés, le CETIAT et CORETEC pourront assister le client dans la mise en œuvre de ses projets.