Projet clés en main : valorisation de chaleur sur fumées de fours verriers
Coretec réalise un projet décarbonation clés en main pour OCV à Chambéry :
Mise en œuvre d’une récupération de chaleur fatale sur les fumées de fours pour alimenter les séchoirs usine.Les acteurs du projet
L’usine d’Owens Corning (OCV) à Chambéry (73) produit de la fibre de verre pour de nombreux domaines et essentiellement pour l’automobile et l’électronique industrielle.
ENGIE COFELY réalise l’exploitation des installations d’eau chaude et de froid pour l’usine.
CORETEC accompagne les sites industriels sur les installations d’utilités process et d’optimisation énergétique (Expertise, ingénierie et réalisations).
Le site
Le site de Chambéry, vendu à FYSOL au 1er trimestre 2022, appartenait à la branche composite du groupe Owens Corning, leader mondial des solutions en fibre de verre depuis + de 75ans.
Depuis 1950, l’usine de production ainsi que le centre de R&D étaient implantés à Chambéry.
Le site fonctionne en 5×8 et a une capacité de production de 90 000 Tonnes annuel.
Concernant la production, il fabrique des WUCS ou des DUCS, qui sont des fils coupés à base de fibres de verre, séchés ou non.
Process de fabrication :
Des matières premières vitrifiables sont mélangées avant d’être envoyées vers les fours verriers pour les faire fondre.
Elles s’écoulent ensuite via des canaux et des filières pour être refroidies.
Une fois refroidie, la matière se solidifie sous forme de filaments et se dirige vers les coupeurs et sécheurs pour lui donner sa forme.
Contexte
Initiation du projet
Le projet est né début 2020, suite à un plan d’actions européen du groupe OCV appelé « convergence », qui fixe les objectifs environnementaux à horizon 2030. Ce plan d’actions est basé sur 5 objectifs, dont, la réduction de 50% des émissions totales de CO2.
L’installation
Le site est équipé de 2 fours (Bissy 1 et Bissy 2) pour la production du verre avant qu’il ne soit transformé en fibre de verre.
Les calories de ces 2 fours sont collectées et renvoyées à l’atmosphère après le traitement des fumées. Des systèmes de récupération d’énergie sont installés sur ceux-ci, mais sont non fonctionnels.
Par ailleurs, l’usine consomme de l’énergie pour les séchoirs, qui servent à enlever l’humidité de la fibre de verre avant traitement thermique.
Demande
Les responsables techniques d’OCV souhaitaient étudier un projet de mise en œuvre d’un système de récupération d’énergie sur les fours Bissy 1 et 2 afin d’alimenter 1 ou plusieurs séchoirs.
C’est dans ce cadre, et par l’intermédiaire d’ENGIE, que nous avons été sollicité pour réaliser, dans un premier temps, une étude de faisabilité, qui a donné suite à des travaux de récupération de chaleur fatale.
Objectif du projet
Récupérer la chaleur fatale sur les fumées des fours et la valoriser en préchauffant l’air entrant des séchoirs et ainsi réduire la consommation de gaz dans le processus de séchage.
L’installation consiste en la mise en œuvre d’un récupérateur sur les fumées des 2 fours verriers, la réalisation d’un réseau d’eau surchauffée qui distribue cette énergie et la mise en place de 11 batteries de préchauffage d’air en amont des séchoirs de l’usine.
Déroulement du projet clés en main
Le projet s’est déroulé sur une période de 2 ans.
L’identification de la source de chaleur fatale et des différents puits de valorisation avaient déjà été réalisée par OCV.
Étude de faisabilité (premier semestre 2020)
Notre mission : Réaliser une étude de faisabilité de récupération de chaleur fatale des fumées des fours verriers.
Celle-ci a permis, à partir des données instrumentées et des mesures ponctuelles qui avaient été faites, de :
- Réaliser les bilans thermiques des sources de chaleur (fours verriers) et des puits de chaleur (séchoirs).
- Vérifier l’adéquation entre les gisements (fumées des 2 fours) et les besoins de chaleur (énergie pour réchauffer l’air au niveau des séchoirs) en termes de puissance, de température, de simultanéité, …
- Définir des solutions en termes de faisabilité technique : dimensionnement équipements, implantation, budgets, performance, …
- Consolider les aspects techniques de faisabilité et les volumes énergétiques en jeu
- Réaliser les documents d’ingénierie préliminaire : schéma PID, plan projet d’implantation…
- Analyser les financements potentiels pour le projet (fonds chaleur, CEE…)
- Budgéter le projet et analyse le planning de réalisation en tenant compte des contraintes de fonctionnement continu des fours.
Campagne de mesure (septembre 2020)
L’étude a identifié que des hypothèses devaient être confirmées. Pour cela, une campagne de mesure complémentaire sur un des 2 fours a été réalisé afin de valider les compositions des fumées, chargée en poussière et polluants.
L’enjeu était de consolider les données d’entrée et lever les incertitudes sur le projet.
Contractualisation (fin année 2020)
Proposition d’une offre consolidée avec un engagement de performances.
Réalisation (début 2021)
Lancement du projet, des études d’exécution et des approvisionnements de matériels (notamment récupérateur principal).
Principe de la solution :
- Mise en place d’un récupérateur : batterie fumée/eau surchauffée de 1,5 MW, pour capter l’énergie dans les fumées.
- Réalisation d’une boucle eau surchauffée pour alimenter les séchoirs
- Mise en œuvre de 11 émetteurs en amont des séchoirs : Intégration de 11 batteries de récupération de 215 KWu eau surchauffée / Air
Spécificité du projet :
Le récupérateur est un générateur de vapeur au sens de la DESP et CORETEC a réalisé son marquage CE, validé par un organisme notifié.
Problématiques de mise en œuvre :
- Process continu :
- Délai d’intervention en arrêt court pour la connexion du récupérateur sur les gaines existantes
- Mise en place des batteries sur chaque séchoir avec arrêt court un séchoir après l’autre
- Manutention récupérateur : Espace exigu pour la mise en place du récupérateur pesant 9T à vide
- Contraintes de travail sur site : Nombreuses manutentions manuelles, température dans la zone de travail…
Mise en service (octobre 2021)
La phase de mise en service s’est déroulée sur une période de 3 semaines environ.
Préparation en amont :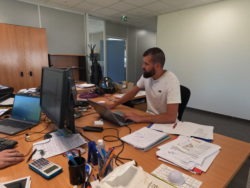
- Programmation de l’automate et élaboration de l’analyse fonctionnelle
- Étude électrique pour fabrication des armoires
- Achat de l’instrumentation et des équipements de contrôle / régulation :
- Armoire des communs (gère alimentation des différentes pompes et instrumentation)
- Automate (gère le fonctionnement et la régulation de l’installation)
Sur site : 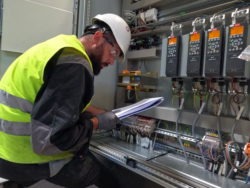
- Mise en service d’un skid maintien de pression, skid de circulation eau surchauffée, échangeur fumées eau surchauffée, skid eau surchauffée air (11 skids)
- Test boucle, test sécurité, essais fonctionnels
- Mise en service de l’installation et mise en production industrielle
- Phases d’ajustements des paramètres de régulation en exploitation
Un des enjeux était le risque de perturbation du process, étant donné que l’on s’intègre directement à l’intérieur et pendant son fonctionnement (fours et sécheurs sensibles).
Au regard des résultats, la phase de mise en service s’est bien déroulée et aucune perturbation du process n’a été constaté.
Mise en exploitation et vérification des performances (fin d’année 2021)
Suite à la mise en exploitation, nous avons été mandatés par OCV pour analyser des données de l’instrumentation mise en place sur l’installation : compteur d’énergie, températures fumées et eau surchauffée, débit eau surchauffée…
Une campagne de mesures ponctuelle a également été réalisée sur les débits de fumées des 2 fours de fusion pour avoir des données complémentaires.
Ces vérifications ont permis d’identifier des pistes d’amélioration, donnant suite à des travaux d’optimisation lancés sur début 2022.
Projet en quelques chiffres
Consommation du site de Chambéry : environ 265 000 MWh par an. (en 2021)
Ce projet devait permettre un gain de 13 500 MWh de gaz sur une base de production de 85 000 Tonnes par an.
Ce qui représente une diminution de l’empreinte carbone de 2 685 Tonnes de CO2, soit une réduction de 7% des émissions de gaz à effet de serre par rapport à 2018, ainsi qu’un impact sur l’indicateur de performance énergétique d’OCV avec une baisse de 0,16 MWh par tonne de produit fini.
Projet nécessitant un CAPEX d’environ 1 000 K€ et un temps de retour sur investissement de 35 mois. (Calculé à partir du coût des énergies en 2020)
Subventions
2 types de subventions ont été obtenues :
L’ASP (aide dans le cadre du plan de relance) : 81 000€
Le projet a été financé par le gouvernement dans le cadre du plan de relance, cette subvention est cumulative avec les CEE.
Les CEE (certificats d’économies d’énergie)
Opération spécifique sur le site qui est soumis aux quotas de CO2 et certifié ISO 50 001.
Le montage du dossier de CEE spécifique est porté par ENGIE SOLUTIONS, qui assure également l’exploitation de l’installation de récupération de chaleur.
Bilan de l’opération
L’installation est en service depuis fin 2021.
Celle-ci est fiable et ne perturbe ni le process, ni les fours.
Sur certains produits, il a même été remarqué une amélioration de la qualité de la coloration du fil au niveau des séchoirs, qui serait, selon l’hypothèse d’OCV, dû au fait que l’air de séchage pré-chauffé contient moins de gaz de combustion et donc améliore la qualité de coloration dans certains cas.
Performances
Au niveau des performances attendues, elles sont 20% en dessous de ce qui avait été annoncé soit 10 800 MWh, dû à :
- Un débit de fumée plus faible après le changement du mode de pilotage d’un des fours (augmentation de la part électrique par rapport à la part gaz).
- Une chute de température plus forte que ce qui était attendu au niveau du traitement des fumées (infiltrations d’air froid refroidissant trop fortement les températures des fumées), l’exploitant étant obligé de bipasser une partie de l’échangeur pour éviter que les fumées condensent et détériorent le traitement de ces fumées.
L’augmentation du coût du gaz et du CO2 depuis fin 2020 compense largement les moindres performances en termes de temps de retour sur investissement.
Des travaux d’amélioration de calorifuges, en aval vers la récupération du filtre à manche, ont été réalisé pour améliorer la récupération possible.
Innovation
Ce projet est innovant de par sa spécificité et la rapidité de sa mise en œuvre. Il est le résultat de l’association de plusieurs composantes indispensables pour la mise en œuvre et la réussite d’un projet de récupération de chaleur fatale :
- Une volonté forte des équipes d’OCV pour réaliser un projet et récupérer l’énergie contenue dans les fumées des fours
- L’apport d’ENGIE pour sa connaissance des installations existantes client, le financement du projet et l’exploitation de cette nouvelle installation de récupération de chaleur
- L’expertise technique de CORETEC permettant de sécuriser le projet et l’installation en termes de fiabilité et de performance
Décarbonation
Un projet qui s’inscrit pleinement dans le plan d’actions européen « convergence » du groupe OCV, fixant des objectifs environnementaux à horizon 2030. Sur les 50% de réduction des émissions totales de CO2 attendus, déjà 7% ont été fournis.
Une première marche est franchie dans la démarche vertueuse d’OCV.
Coretec participe à ce projet en apportant son expertise et sa compétence de mise en œuvre pour valoriser l’énergie fatale des fours en interne, permettant ainsi d’éviter un rejet de 10 800 MWh de gaz par an dans l’atmosphère.
Références similaires