Audit énergétique réglementaire pour l’un des sites chimiques de POLYNT
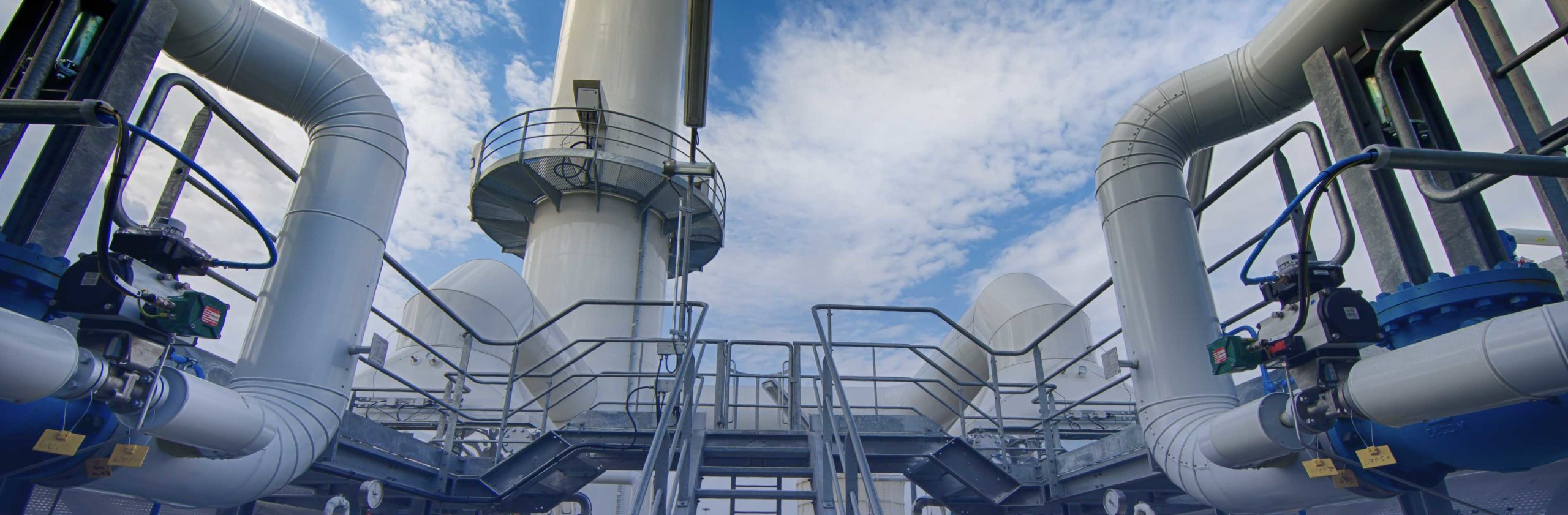
CONTEXTE
POLYNT est un groupe international, implanté en France à Drocourt (62), spécialisé dans la production chimique des polymères intermédiaires et des composites. Le groupe possède 2300 salariés dans le monde, dont environ 200 sur son site de Drocourt.
Le site POLYNT Composites, situé dans le Nord de la France, assure principalement la production de polyester et de résine. Il est soumis à l’imposition réglementaire de l’audit énergétique dans le cadre de son activité.
Dans ce contexte, le responsable technique du site a sollicité Coretec afin de réaliser une prestation d’étude permettant de renouveler son audit énergétique. Au-delà d’une contrainte réglementaire, cet audit est l’opportunité d’améliorer la performance énergétique du site en ciblant ses principaux consommateurs. Les prestations d’audit énergétique réalisées par Coretec permettent d’obtenir des préconisations techniques concrètes et de pouvoir passer à l’action pour les industriels.
CADRE DE L’ETUDE
DESCRIPTIF
Dans le cadre de cet audit énergétique, l’ensemble des procédés de fabrication et des utilités du site ont été étudié. L’objectif de cette démarche étant de déterminer la répartition énergétique du site et d’identifier les plus gros consommateurs. Un plan d’action est ensuite établi, permettant d’apporter des améliorations vis-à-vis des consommations énergétiques.
L’audit s’est déroulé sur une période de 3 mois et se basait sur l’année 2022 en référence, une année pleine et représentative.
FOCUS SUR L’ETUDE REALISEE
ÉTAT DES LIEUX ENERGETIQUE DU SITE
POLYNT Composites est un site d’environ 20 bâtiments composé de bureaux et unités de production.
L’installation fonctionne en 5×8. Elle est arrêtée 2 semaines durant la période estivale et une semaine sur la période hivernale pour les opérations de maintenance.
Pour assurer sa production, le site est composé de différentes zones :
- 3 bâtiments de bureaux
- 3 ateliers de production
- Plusieurs zones de stockage
Les énergies primaires utilisées sur le site sont l’électricité, le gaz naturel et le fioul.
BILANS ENERGETIQUES
Les bilans énergétiques ont permis de mieux comprendre le fonctionnement des installations du site et notamment que l’usine, en fonctionnant à pleine charge, est plus performante et conduit à des indices de performance énergétique (IPE) plus optimisés du fait de l’effet « talon » des consommateurs énergétiques.
La répartition globale des consommations du site se définie comme suit :
- 60% de consommations de gaz naturel,
- 35% de consommations d’électricité,
- 5% de consommations de fioul domestique.
On constate également l’impact fort de la hausse des coûts de l’énergie sur les dernières années avec une facture de gaz multipliée par 5 entre 2021 et 2022 et une facture électrique en hausse de plus de 40% pour une même consommation.
ACTIONS D’AMÉLIORATION DE LA PERFORMANCE ENERGETIQUE (AAPE)
Sur les 20 propositions qui avaient été faites lors du précédent audit énergétique de 2018, 7 ont été réalisées entre temps ou sont en cours de réalisation :
- Récupération des condensats vapeur
- Modification de la programmation horaire du compresseur
- Ajout de compresseur à vitesse variable en remplacement d’un ancien
- Remplacement d’équipements d’éclairage énergivores par des LEDs
- Remplacement de médias filtrants des compresseurs
- Récupération de la chaleur des compresseurs pour chauffer le local osmoseur en hiver
Dans le cadre de la prestation de diagnostic énergétique réalisée par Coretec, 20 solutions ont également été envisagées pour l’industriel.
D’un côté, des propositions complexes nécessitant de forts investissements, permettant des réductions financières et énergétiques plus ambitieuses (investissement entre 500k€ et 1.5M€ pour des TRI au-delà de 7 ans).
D’un autre côté, des solutions plus simples et moins coûteuses permettant d’optimiser les consommations du site industriel de manière moins importantes. Dans ce cas, les solutions proposées nécessitent un investissement moindre, pour des temps de retour sur investissement « courts ».
Au-delà des importants défis de décarbonation auxquels les industriels sont confrontés, il est crucial de comprendre que toutes les solutions, même celles offrant des gains modestes, peuvent contribuer à leur transition énergétique. En effet, chaque réduction, aussi minime soit-elle, est un pas vers la neutralité carbone. Si certains industriels rencontrent des difficultés à débloquer des investissements conséquents, ils peuvent néanmoins débuter par de petites initiatives avant d’adopter des mesures plus ambitieuses.
Parmi ces solutions, en voici 4 que nous vous présentons :
- Solutions « complexes » :
- Rehausse du point de rosée d’un sécheur pour le porter à 20°C
- Optimisation taux d’O2 de 2 des chaudières
- Solutions « simples » :
- Préchauffage de l’air comburant d’une des chaudières
- Mise en place d’une PAC sur TAR pour chauffage des locaux de production
FOCUS SUR 4 SOLUTIONS D’AMÉLIORATION DE LA PERFORMANCE ENERGETIQUE
- 1 : Rehausse du point de rosée d’un sécheur à -20°C,
- 2 : Optimisation du taux d’O2 de 2 chaudières,
- 3 : Préchauffage de l’air comburant d’une chaudière,
- 4 : Mise en place d’une PAC sur TAR pour chauffage de locaux de production.
Solution 1 : Rehausse du point de rosée d’un sécheur à -20°C
Principe de la solution :
Le point de rosée de l’installation d’air comprimé de l’atelier étudié est réglé à environ -60°C alors que les consommateurs ne nécessitent pas une telle qualité de séchage et qu’un point de rosée à -20°C est largement suffisant. Cette opération nécessite seulement de modifier la consigne de point de rosée sur le sécheur.
En quelques chiffres :
Une solution qui permet un gain énergétique d’environ 40MWh d’électricité /an, soit une économie financière d’environ 4,5k€ annuel.
Côté impact environnemental, elle permet d’éviter l’émission de 2 tonnes de CO2 chaque année.
Au niveau du budget, elle représente un CAPEX proche de 0k€ pour un TRI immédiat.
Solution 2 : Optimisation du taux d’O2 de 2 chaudières
Principe de la solution :
En analysant les tickets de combustion, Coretec a remarqué que le taux d’O2 n’était pas optimisé sur la chaudière.
La solution proposée consiste à améliorer les réglages de combustion du brûleur de la chaudière fluide thermique en réduisant le taux d’O2. Cela aura pour conséquence de réduire la quantité d’air chauffée inutilement et donc de réduire la consommation de gaz naturel.
La mise en œuvre de la solution consiste à faire intervenir un technicien brûleur pour reprendre le réglage de combustion.
En quelques chiffres :
Une solution qui permet un gain énergétique d’environ 65MWh de gaz /an, soit une économie financière d’environ 4k€ annuel.
Côté impact environnemental, elle permet d’éviter l’émission de 15 tonnes de CO2 chaque année.
Au niveau du budget, elle représente un CAPEX d’environ 1k€ pour un TRI immédiat.
Solution 3 : Préchauffage de l’air comburant d’une chaudière
Principe de la solution :
Elle consiste à mettre en place un échangeur entre les fumées et l’air comburant de la chaudière afin de préchauffer l’air comburant. Néanmoins, avec le brûleur existant, l’émission de NOx serait plus importante et la chaudière est déjà à la limite des seuils autorisés. Nous avons donc proposé de changer le brûleur pour un bruleur bas NOx intégrant un fonctionnement avec de l’air préchauffé.
En quelques chiffres :
Une solution qui permet un gain énergétique d’environ 930MWh/an, soit une économie financière d’environ 56,5k€ annuel.
Côté impact environnemental, elle permet d’éviter l’émission de 210 tonnes de CO2 chaque année.
Au niveau du budget, elle représente un CAPEX d’environ 500k€, avec une aide CEE estimée à environ 83k€, pour un TRI supérieur à 7 ans.
Solution 4 : Mise en place d’une PAC sur TAR pour chauffage des locaux de production
Principe de la solution :
Elle consiste à mettre en place une boucle d’eau chaude pour réaliser une partie du chauffage des locaux de production actuellement fait à la vapeur. Pour cela, nous avons proposé de récupérer de l’énergie sur le retour du réseau de TAR et de rehausser le niveau de température via une pompe à chaleur qui alimentera la boucle eau chaude.
En quelques chiffres :
Une solution qui permet un gain énergétique d’environ 3 620MWh/an, soit une économie financière d’environ 470k€ par an.
Côté impact environnemental, elle permet d’éviter l’émission de 1100 tonnes de CO2 chaque année.
Au niveau du budget, elle représente un CAPEX d’environ 1 200k€, avec des aides Fonds Chaleur et CEE estimées à 200k€, pour un TRI d’environ 2 ans.
*Pour réaliser les bilans d’investissement des solutions, l’étude prend en compte un coût des énergies de 110€/MWhe (elec), 61€/MWh PCS (gaz naturel) et 82€/MWhPCS (fioul domestique).
BILAN : tableau de synthèse chiffré
Cet audit énergétique réalisé par CORETEC pour le site de POLYNT à Drocourt met en lumière des opportunités significatives d’amélioration de la performance énergétique. Chaque action, qu’elle soit simple ou complexe, contribue à réduire les consommations énergétiques et à avancer vers la neutralité carbone.
Grâce à ces préconisations, POLYNT pourra, non seulement, se conformer aux exigences réglementaires mais aussi optimiser ses processus pour une meilleure efficacité énergétique.
Pour en savoir plus sur nos services d’audit énergétique et découvrir comment nous pouvons accompagner votre entreprise dans sa transition énergétique, n’hésitez pas à nous contacter.